One of the modern and widely used methods in the painting industry is electrostatic powder coating. In this method, unlike traditional liquid painting, powder paint is used with electrostatic technology to coat the surface, and then the paint is fixed at high temperatures. Initially, this technique was only used in limited industries such as automotive and industrial equipment, but with the advancement of technology and reduced production costs, the use of electrostatic powder coating has gradually expanded in various industries.
Electrostatic Powder Coating Services
Alumland Industrial Complex, with years of experience in the field of electrostatic powder coating services and the implementation of hundreds of painting projects, has been able to take a big step towards quality production. The Alum Form electrostatic powder coating unit, with the best equipment and electrostatic painting line and using high-quality powder paint, offers the best services to various industries. We have the ability and possibility to carry out bulk orders in the shortest possible time with reasonable prices.
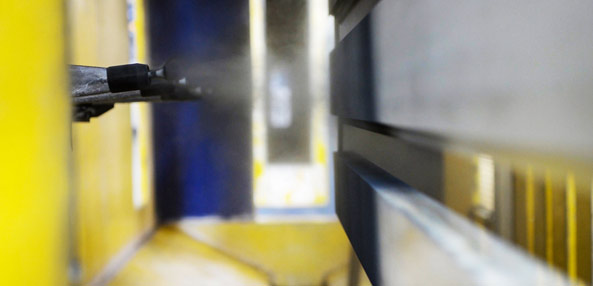
Stages of Electrostatic Powder Coating
The mechanism of electrostatic powder coating is based on the electrostatic attraction of the powder to the metal surface. The electrostatic powder coating process can be summarized in four stages
Surface Preparation: To create better adhesion of the powder to the surface, the surface must first be cleaned and free of any dirt, grease, and rust. This step is often done using chemical or mechanical methods.
Powder Spraying: In this step, the colored powder is sprayed electrostatically onto the surface using spray guns. The spray gun charges the powder, and these charges cause the powder to be attracted to the desired surface.
Curing Process: After spraying the powder, the part is placed in an oven at a specific temperature (between 160 and 200 degrees Celsius). At this temperature, the powder particles melt and create a uniform and resistant coating on the surface.
Final Inspection: After the part is removed from the oven and cooled, the quality of the final surface is checked and it is ensured that the coating is flawless and uniform.
Electrostatic Powder Coating Equipment
The specialized equipment and electrostatic powder coating devices of the Alum Form surface coating and electrostatic powder coating unit are designed to create a uniform and resistant coating on the aluminum surface. The Alum Form electrostatic powder coating line includes:
Electrostatic Powder Spraying Device (Powder Spray Gun): This device is the main tool for spraying powder on surfaces. The spray gun, by creating an electric charge on the powder particles, makes them stick to the metal surface.
Powder Spraying Booth: A special booth where powder spraying is done. This booth is designed in such a way that the powders that do not stick to the surface are collected in a recycled way and returned to the system.
Powder Recycling System: A smart system that collects the extra powders that have not adhered to the surface and prepares them for reuse. This saves materials and reduces costs.
Curing Oven: Ovens where, after spraying the powder, the part is transferred to it so that the powder melts at a temperature between 160 and 200 degrees Celsius and adheres to the surface. Curing ovens are of the conveyor (automatic) or fixed type.
Pre-treatment and Surface Preparation System: This system is used to clean and prepare the surface before powder spraying. Different methods such as chemical washing, acid washing, phosphating, or sandblasting are used to prepare the surface for painting.
Ventilation and Filtration Units: To maintain safety and health in the work environment, air ventilation and filtration units are used to prevent the spread of powder particles in the air.
Control and Monitoring Systems: Controlling equipment that manages and monitors the spraying, curing, and temperature process to ensure the quality and integrity of the coating.
These equipment and devices are fully coordinated with each other to perform the electrostatic powder coating process accurately and efficiently and to achieve high-quality and resistant coatings .for the final products
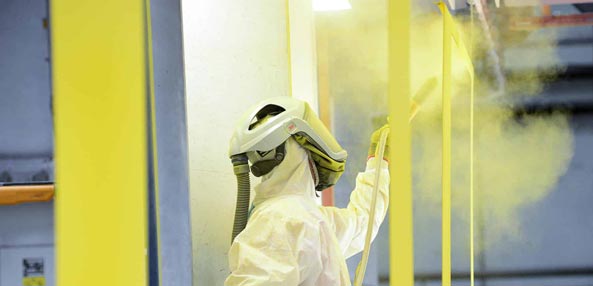
Advantages of Electrostatic Powder Coating
High Durability and Resistance: One of the main advantages of electrostatic powder coating is its high resistance to weather conditions, corrosion, abrasion, and impact. Due to these features, the use of this method in the automotive industry, etc., has increased.
Environmentally Friendly: Unlike liquid paints that contain organic solvents and harmful chemicals, powder paints are VOC-free (volatile organic compounds) and therefore do not harm the environment.
Higher Efficiency: Powder paint is more efficient than liquid paints. In the powder spraying process, if the powder does not stick to the surface, it can be recycled and reused, while this is not possible in liquid paint.
Uniform and Consistent Colors: Due to uniform spraying and precise curing process, electrostatic powder coating creates a uniform, glossy, and beautiful coating that has a higher quality compared to other methods. Powder paints can create a coating with a thickness between 40 and 120 microns. This thickness is obtained uniformly and without creating stains or lines, which results in a glossy and smooth surface.
Variety in Color and Texture: Electrostatic powder paints are produced in a wide range of colors and textures (glossy, semi-glossy, matte, textured). This feature allows manufacturers and designers to use it in various industries such as interior and exterior decoration, automotive, and home appliances.
Resistance to Chemicals: Electrostatic powder coating is highly resistant to chemicals such as acids, bases, and solvents.
Challenges and Limitations of Electrostatic Powder Coating
Despite its many advantages, this method also has challenges and limitations:
Limitations in Use for Non-Conductive Materials: This process is usually used for metal surfaces. Although non-metallic surfaces such as plastic and glass can also be coated using special techniques, these cases are not yet as extensive as metal surfaces.
Need for Special Equipment: The use of this process requires special equipment such as curing ovens and electrostatic spray guns, which can be expensive.
Precise Temperature Control: In the curing stage, precise control of temperature and time is very important. If the temperature or time is not appropriate, the final quality of the paint is affected.
Electrostatic Powder Coating Standard
The electrostatic powder coating standard is a set of instructions and criteria that are determined to ensure the quality and efficiency of powder coatings in various industries. Some of the important standards for electrostatic powder coating are:
ISO 9001 Standard: ISO 9001 standard is one of the most well-known quality standards that is used to ensure the quality of the production process and quality management in powder paint manufacturing plants. This standard ensures that all stages of production are under strict control and are carried out according to specific quality criteria.
ISO 12944 Standard: This standard is specifically designed to protect metal surfaces against corrosion through various coatings, including powder paint. ISO 12944 examines and classifies the level of protection against corrosion based on environmental conditions, and powder paints must demonstrate good resistance against corrosive agents in accordance with this standard.
ASTM D3451 Standard: ASTM is one of the reputable international organizations for material standards and test methods. ASTM D3451 is a set of test methods for the quality and performance of powder coatings, which includes evaluating adhesion, coating thickness, hardness, abrasion resistance, and appearance properties of the coating.
Alum Form Company provides all services related to oven painting with an emphasis on quality and guaranteed services